Geological challenges and environmental clearances remain key hurdles for tunnel projects.
The development of road and railway tunnel projects in India is progressing rapidly, driven by government initiatives like the Bharatmala and Rail Vikas programs. Key projects, including the Zojila Tunnel in Jammu & Kashmir and the Atal Tunnel in Himachal Pradesh,
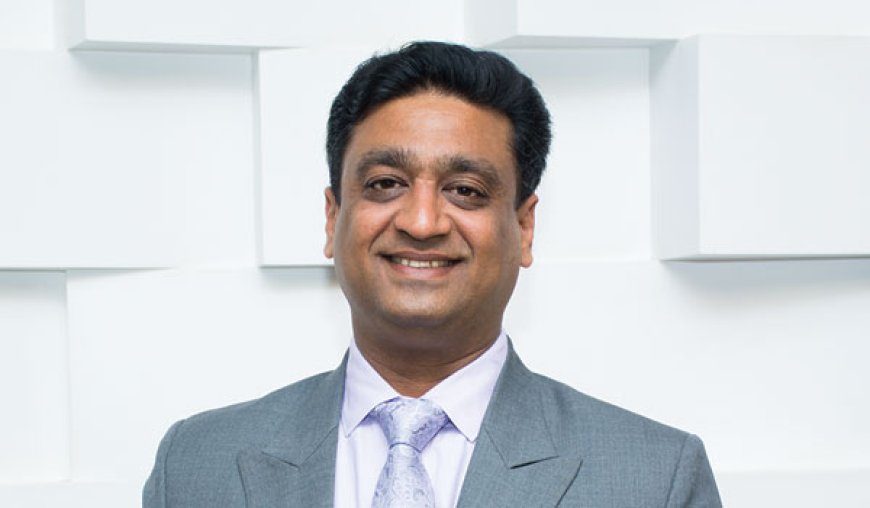
How is the development of road and railway tunnel projects progressing in the country?
The development of road and railway tunnel projects in India is progressing rapidly, driven by government initiatives like the Bharatmala and Rail Vikas programs. Key projects, including the Zojila Tunnel in Jammu & Kashmir and the Atal Tunnel in Himachal Pradesh, are enhancing connectivity in challenging terrains. The Indian Railways is also advancing tunnel construction, notably in the Northeast and Himalayan regions, to improve freight and passenger transport. Advanced tunneling techniques, such as the use of Tunnel Boring Machines (TBMs) and the New Austrian Tunneling Method (NATM), are expediting construction. However, geological challenges and environmental clearances remain key hurdles.
How are underground and mountain tunnel projects helping in creating better connectivity infrastructure?
Underground and mountain tunnel projects are significantly improving connectivity infrastructure by reducing travel time, enhancing safety, and ensuring all-weather accessibility. These tunnels bypass difficult terrains, such as mountains and congested urban areas, enabling seamless transportation of goods and passengers. Projects like the Atal Tunnel and the under-construction Zojila Tunnel provide crucial links to remote and strategic regions, boosting trade and tourism. In cities, metro and road tunnels ease congestion and support sustainable urban mobility. By integrating advanced
engineering techniques, these tunnels strengthen national infrastructure, foster economic growth, and improve resilience against natural disruptions like landslides and heavy snowfall.
How is technology evolving in tunnelling? How are technologies such as TBMs making tunnelling productive and efficient?
Tunneling technology is evolving rapidly, making construction safer, faster, and more efficient. Traditional methods like drill-and-blast are now complemented by advanced techniques such as the New Austrian Tunneling Method and Tunnel Boring Machines.
TBMs, in particular, have revolutionized tunneling by enabling precision excavation with minimal environmental impact. These machines can handle diverse geological conditions, reducing project timelines and improving safety. Innovations like automated monitoring systems, digital twin technology, and AI-driven geological mapping further enhance efficiency. Additionally, advancements in ground reinforcement, ventilation, and waterproofing are improving tunnel durability, ensuring long-term sustainability
What are the major challenges encountered in tunnelling? How are you
Tunneling projects face several major challenges, including geological uncertainties, water ingress, high overburden pressure, and environmental concerns. Unstable rock formations, seismic activity, and soft soils can lead to collapses or construction delays.
Additionally, urban tunneling poses risks to existing infrastructure, while tunnels in hilly terrains must overcome extreme weather conditions.
To minimize these challenges, advanced techniques like geotechnical investigations, real-time monitoring, and predictive analytics are used. TBMs help navigate difficult geology efficiently. Ground freezing, shotcrete lining, and rock bolting strengthen tunnel stability. Environmental impact assessments and sustainable construction practices ensure minimal ecological disruption, making tunneling safer and more efficient.
What are the technologies used for the tunnelling projects?
In TBM tunnelling projects, key technologies utilized include shield tunnelling, automated TBMs, data management systems, embedded cameras, continuous belt conveyors, complex grouting processes for segment sealing, laser guidance, computerized control systems, and specialized shield machines depending on the soil conditions, all aimed at efficient excavation and minimizing disruption to the surrounding environment.
|
|
Key points about these technologies:
Shield tunnelling: Particularly important in soft ground conditions, where a shield mechanism supports the tunnel face while excavation occurs, preventing collapse.
Automated TBMs: Modern TBMs incorporate automated controls with sensors and data analysis to optimize excavation and minimize human intervention.
Data management systems - help manage and administer operational procedures for tunnelling projects.
Embedded cameras - provide 3D mapping for TBMs.
Continuous belt conveyors: Used to efficiently transport excavated material from the tunnel face to the surface, often with long, single conveyor flights for large projects.
Grouting process: A complex mix of cement, bentonite, and other materials is used to fill gaps between tunnel segments and the shield, ensuring stability.
Laser guidance and computerized controls: Enhance accuracy and precision during tunneling operations.
Other technologies
Automatic tailskin clearance measurement system: SLuM is a system that
measures the ring position relative to the tailskin axis with millimetre accuracy and fully automatically.
TUnIS ring sequencing system: This system automatically calculates the optimum ring sequence for tunnel advances that include segmental lining.
Microtunneling: A process that uses a remotely controlled microtunnel boring
machine (MTBM)
Sequential excavation method (SEM): A progressive excavation technique used to mine out specific sections of a tunnel
Shotcrete: A construction technique that involves spraying a mixture of cement and other materials
Automation and digitalization are increasingly proving to be drivers in mechanized tunneling technology. They complement the successes achieved in recent decades in coping with more difficult ground conditions, higher support pressures, larger diameters and greater tunnel lengths as well as in increasing performance and efficiency. They are also proving to be achievable only through discussion and cooperation between the various stakeholders – on
Three drivers in particular, presented below, are determining new development approaches for mechanized underground construction: Automation including artificial intelligence (AI), Sustainability-focused further development of systems for the treatment of water and slurry, and
These drivers enable further steps toward greater safety, quality and efficiency against the backdrop of the required sustainability and the lack of qualified personnel for the successful realization of tunnelling projects.
What is your view on India’s tunnelling sector in the coming years?
India’s road tunnelling sector faces significant challenges due to rugged terrain, seismic activity and extreme weather, particularly in the Himalayan and north-eastern regions. These factors drive up costs and complexity, and demand advanced engineering, skilled labour and strict environmental management. However, with substantial growth anticipated through government initiatives and increased connectivity demands, strategic investments in research and development, smart systems and sustainable practices are crucial.
Strengthening public-private partnerships and enhancing workforce skills will be essential to overcoming these challenges, ensuring that India builds world-class infrastructure that promotes economic growth and improves road standards.
years. From $28.89 billion in 2025, it is expected to grow to $37.78 billion in 2029 at a compound annual growth rate (CAGR) of 6.9%.
Box
Key tunnelling projects by J Kumar
Completed projects
Delhi Metro: CC-20, CC-24, DC-08
Mumbai Metro: Line 3 Pkg 5 & 6
Ongoing underground projects
Mumbai Metro: Line -7A
Delhi Metro: DC -08
Surat Metro: CS-03
Upcoming projects
Maharashtra Metro Rail Corporation Ltd project
Design and construction of underground station at Market Yard, Padmavati, Katraj and associated tunnels at North South Corridor of Pune Metro Rail Project. Approx. Est. cost: Rs 2,000 cr.
5.46 km metro tunnel By TBM tunnel and 3 underground stations.
MMRDA and CIDCO projects
Metro Line 8, also called the Gold Line, to connect Chhatrapati Shivaji Maharaj International Airport (CSMIA) in Mumbai with Navi Mumbai International Airport (NMIA). The route will pass through key areas like Kurla and Mankhurd, linking Lokmanya Tilak Terminus and a proposed Interstate Bus Terminal at Mankhurd.
Approx. Est. cost of Line 8: Rs. 15,000 cr; Approx. Est. cost of tunnel: Rs 3,000 cr
Metro Line 8 will span 35 km, comprising 25.8 km of elevated track and 8.2 km of underground sections by TBM. It will include 20 stations and integrate with Metro 2B.
MMRDA project
Metro Line 11 has been proposed to extend the Green Line southward from Wadala to Chhattrapati Shivaji Maharaj Terminus. Approx. Est. cost: Rs 4,000 cr
The entire Line 11 is of 12.774 km. It will consist of an 8.765 km underground stretch by TBM and 10 stations.
Maharashtra Metro Rail Corporation Ltd project
Thane Metro Phase 1 project with one circular line and 22 stations is a 29 km mass rapid transit system. Approx. Est. cost of entire phase 1 is Rs 12,200 cr. Approx. Est cost of tunnel: Rs 1,100 cr. Elevated (primarily) and underground (2-3 km) having 2 underground stations by TBM.
Bruhat Bengaluru Mahanagara Palike (BBMP) project
Constructing a 16.5-km tunnel road connecting Central Silk Board and Hebbal by combination of NATM and drill & blast method. Approx. est. cost: Rs 17,780 cr. In the second phase, a tunnel road is proposed between KR Puram and Nayandahalli, called east-west corridor. Both the projects are estimated to cost Rs 50,000 crore.
MMRDA project
New access controlled 8-lane highway to connect Kalyan, Dombivali, Ulhasnagar, Ambernath, and Badlapur to Mumbai, Navi Mumbai and the upcoming Navi Mumbai International Airport.
The highway will be 20 km long, having 13.65 km at ground level, tunnel of 3 km by combination of NATM and drill & blast method, and viaduct of 3.95 km.
NHIDCL projects
Vailoo Tunnel project in Jammu and Kashmir. The tunnel will run under Sinthan Pass on NH-244. Approx. est cost: Rs 3,500 cr
Construction of uni-directional Sudhmahadev – Dranga Twin Tube Tunnel and its approach roads on Chenani – Sudhmahadev – Goha road including uni-directional Tunnel-1 and Tunnel 2 on NH-244 in the union territory of Jammu and Kashmir. Approx. Est Cost: Rs. 2,500 cr.