Leveraging a new benchmark in green steel production
As industries push for cleaner alternatives, breakthrough technologies are shaping the future of green steel. Hydrogen-based steelmaking, particularly Direct Reduced Iron (DRI) using green hydrogen, eliminates CO₂ emissions by replacing coal with hydrogen, producing only water vapour.
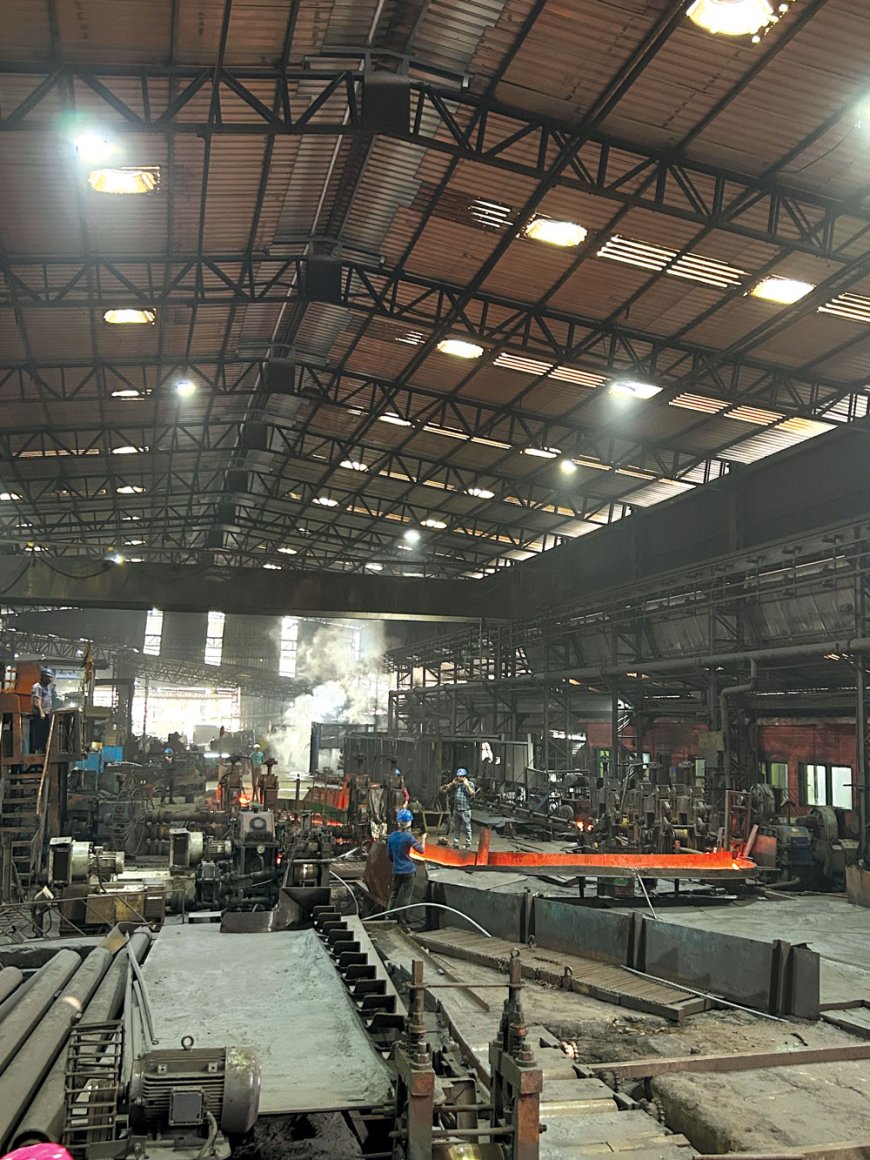
The global push for sustainability has permeated every sector, but few industries face as critical a challenge and opportunity as the steel industry. Steel is the backbone of modern civilization, forming the foundation of towering skyscrapers, intricate transportation networks, and the vehicles we drive. However, its ubiquity comes at a cost, accounting for 7-9% of global CO₂ emissions annually. As the urgency to combat climate change intensifies, the steel industry is undergoing a transformative shift toward green steel production an innovation poised to revolutionize not just manufacturing, but also the future of infrastructure, energy, and technology.
Traditional methods and green steel technologies
The traditional methods of steel production have long been reliant on fossil fuels, primarily coal and coke, which result in the emission of vast amounts of carbon dioxide. However, new green steel technologies offer a promising path to decarbonizing this heavy industry. Green steel production seeks to replace carbon-intensive processes with low-carbon or carbon-free alternatives, aligning with global sustainability goals and making significant strides toward mitigating the environmental impact of steel manufacturing.
As the world turns its attention to decarbonization, green steel is emerging as a key player in the broader efforts to reduce greenhouse gas emissions. India, as the world's second-largest steel producer, is at the forefront of this shift, with green steel technologies playing a key role in realizing the nation's ambitious net-zero by 2070 goal.
The green steel solution: Circularity and renewable energy
Steel’s strength, durability, and recyclability make it a cornerstone of modern infrastructure, but the material’s potential for circularity makes it vital for a sustainable future. The concept of circular steel produced using renewable energy sources like solar, hydro, and wind is gaining traction. This approach involves recycling and reusing steel in a closed-loop system, drastically cutting emissions.
However, India’s steel recycling rate remains well below the global average of 85%, with only about 20% of steel in FY22 produced using domestic and imported scrap. Despite the introduction of the National Steel Scrap Recycling Policy in 2019, substantial investments are still needed to strengthen the scrap supply chain and enhance circularity in the sector.
To accelerate this transition, the Indian government has launched key initiatives such as the Production-Linked Incentive (PLI) scheme and the Green Steel Mission, which has been allocated Rs 15,000 crore are driving investments and fostering innovation. This is evidenced by the Rs 27,106 crores in committed investments under the PLI scheme, expected to produce 7.9 million tons of specialty steel and generate 8,660 jobs by 2024. The Indian government is also promoting circular steel production through the Steel Scrap Recycling Policy, which aims to reduce imports and optimize the use of domestic scrap.
Breakthrough technologies in green steel production
As industries push for cleaner alternatives, breakthrough technologies are shaping the future of green steel. Hydrogen-based steelmaking, particularly Direct Reduced Iron (DRI) using green hydrogen, eliminates CO₂ emissions by replacing coal with hydrogen, producing only water vapour. Electrolytic reduction, leveraging renewable electricity, offers another zero-carbon alternative by separating iron from ore without fossil fuels.
Meanwhile, Electric Arc Furnaces (EAFs) are gaining traction in India with Tata Steel UK announcing that its proposals to deliver a state-of-the-art Electric Arc Furnace for greener steelmaking in Port Talbot has got the requisite approval from the local council. This is a major step in the promotion of circular manufacturing by recycling steel scrap and reducing reliance on virgin iron ore and coal. Additionally, Carbon Capture, Utilization, and Storage (CCUS) is emerging as a promising solution to curb emissions from traditional steelmaking. With India ranking as the world’s second-largest steel producer—and the sector contributing nearly 12% of the country’s industrial emissions—these innovations are essential for aligning economic growth with sustainability.
The market for green steel: Powering the future
The demand for green steel is set to rise sharply. India’s current crude steel production capacity of 179.5 million tons is expected to reach 300 million tons by 2030, presenting a significant opportunity for companies to adopt sustainable technologies. The global green steel market, valued at $718.3 billion in 2024, and estimated to reach $766,763 million by 2030 is projected to grow at a CAGR of 6%, driven by automotive, renewable energy, and construction industries.
Green steel plays a critical role in enabling next-generation technologies. As the world transitions toward electrification, industries are increasingly turning to electric vehicles and sustainable infrastructure. Whether in EV chassis, renewable energy components, or robotics, steel remains indispensable. Green steel, therefore, is not just a solution for sustainability; it is a key enabler of the technologies that will power the future.
Post COP21, signatory nations gained greater clarity on their bureaucratic expectations and financial obligations, while COP26 marked a breakthrough with the agreement on the contentious Article VI, known as "Loss and Damages." Beyond financial commitments, COP26 also reinforced the urgency of decarbonization through initiatives like the Glasgow Agenda, and the Global Coal to Clean Energy Transition, backed by more than 40 countries. India's commitment to a sustainable future is evident in the increasing collaboration between the public and private sectors to accelerate green steel production.
Environmental and economic implications
The environmental benefits of green steel production are immense. Green steel significantly reduces carbon emissions envisioned to 1.3 tCO2 /TCS by 2047, aligning with global sustainability targets and helping industries transition to cleaner, renewable energy sources. It also supports the circular economy by reusing steel scrap, which further reduces environmental impact.
From an economic perspective, the transition to green steel presents both challenges and opportunities. Financial mechanisms such as green bonds, blended finance, and concessional loans help de-risk investments and attract private capital. By bridging funding gaps, especially in early-stage and high-risk sectors, effective financing ensures that climate goals are met in a timely and efficient manner, promoting a transition to a low-carbon, sustainable economy. While the initial investment in developing and scaling these technologies is substantial, the long-term advantages are clear. As green steel production methods advance and become more efficient, costs are expected to decline, making it increasingly competitive with conventional steel.
It is estimated that achieving net-zero emissions in India’s steel sector will require an investment of Rs 16 to 22 lakh crore, though these projections pertain solely to the steel industry. The rising demand for sustainable materials presents a significant market advantage for green steel producers. Companies that invest early in green steel technologies will be well-positioned to tap into the expanding green economy, securing a competitive edge in a market that is becoming increasingly eco-conscious.
The choice is stark: persist with outdated methods and inherit a destabilized planet, or embrace green steel as the cornerstone of a sustainable industrial era. Sceptics may argue for incremental change, but the urgency of climate collapse demands radical action. Let us build a world where skyscrapers and bridges stand not as monuments to excess, but as testaments to human ingenuity and stewardship. The future is not low-carbon; it is zero-carbon, and green steel lights the path.