Aluminium is making its presence felt as a formwork material of choice.
Abhijit Ashok Acharya General Manager, MEVA Formwork Systems How are the applications of formworks evolving in the latest construction projects? Any concrete structure per se, cannot be built without formwork. In our country, most of the formwork used has been the traditional or conventional systems using steel plates, wooden members, etc. However, as structures evolve
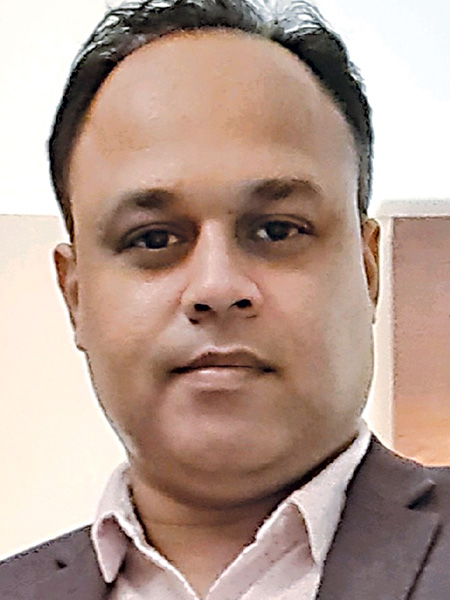
Abhijit Ashok Acharya
General Manager, MEVA Formwork Systems
How are the applications of formworks evolving in the latest construction projects?
Any concrete structure per se, cannot be built without formwork. In our country, most of the formwork used has been the traditional or conventional systems using steel plates, wooden members, etc. However, as structures evolve in their complexity, timelines become more stringent, jobsite safety gains importance, the formwork has also evolved with the demand for engineered systems increasing. Steel plates have given way to proprietary panel systems, cup lock and steel cribs have given way to designed shoring systems, and aluminium is making its presence felt as a formwork material of choice.
What are the latest technologies and solutions offered by the company?
MEVA has always been a big believer in innovative products, which are easy to use, long lasting and the most economical in terms of cost per repetition. Our column and wall panel systems are based on a common global platform of hollow rolled profile. We see in today's market scenario that many well known companies with the sole purpose of cutting costs, are compromising on durability and concrete finish, whereas MEVA has been constantly upgrading the market. The closed hollow profile provides durability, very high resistance to jobsite wear & tear, and extends life of the facing, thus keeping cost per reuse to the bare minimum.
MEVA's automatic climbing system, which is our flagship product globally, offers cycle times of even 5 and 6 days, completely eliminating the use of a crane. When the formwork industry in India was fixated on plywood-based panel systems for slabs, we moved towards a complete aluminium finish, thus eliminating the need for replacing the facing every few repetitions.
What are the major features of your products?
Lowest cost per repetition, through durability, negligible costs during the product life cycle, ease of use and high levels of modularity are the main product characteristics, whichever MEVA product one chooses for their construction project.
How do you cater to the changing customer needs with the project size and designs are changing?
Our slab formwork system, MonoDec has interchangeable panels with the wall formwork system, MonoWall. Our universal wall and column formwork system, the EcoFix has panels and accessories which can be used for any column and wall dimensions. The above systems can be used for any kind of project, across industry type, thus minimising the customer's repurchase budget. Our climbing formwork, the MSC240 can be used for platforms to suit residential, commercial buildings as well as bridge piers and dam projects. The components of our Slab Table formwork can be interchanged with our MBS columns formwork.
How do you look at the future market opportunities? What are your expansion plans?
The MEVA management in Germany takes India very seriously. India is a focus market for the company and we clearly are here for the long haul. In the past three years, MEVA India has launched three products which cater to almost 50% of our current annual sales. More products are in the pipeline. We are very bullish on India and are completely in sync with the Prime Minister's initiative of Make in India. India is now part of the global supply chain of the company. You will hear a lot in this space in the years
to come.
Hits: 0