Implementation of OMNICOMM gives up to 30% savings in fuels and lubricants
Fuel costs for the construction equipment compile up to 50% of operating costs and companies most likely aren't managing these expenditures optimally. The need for the construction companies in fuel and lubricants can be reduced by at least a third while maintaining the full scope of work, and this is a good way to increase efficiency in the construction industry. And this is not only fuel costs what can be optimized. As many as 35% per cent of the companies who implemented the fuel & fleet management solutions see performance increase and 15% of the companies track maintenance cost reduction. So, if you want to be competitive, you need to install solutions that will help you in your fleet management.
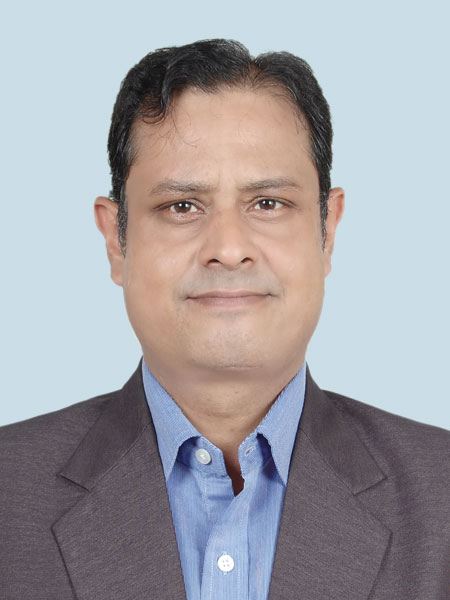
- SURJODOY GHOSH
Managing Director, OMNICOMM in India
How important is optimizing the use of fuel in the current scenario?
Fuel costs for the construction equipment compile up to 50% of operating costs and companies most likely aren't managing these expenditures optimally. The need for the construction companies in fuel and lubricants can be reduced by at least a third while maintaining the full scope of work, and this is a good way to increase efficiency in the construction industry. And this is not only fuel costs what can be optimized. As many as 35% per cent of the companies who implemented the fuel & fleet management solutions see performance increase and 15% of the companies track maintenance cost reduction. So, if you want to be competitive, you need to install solutions that will help you in your fleet management.
What are the fuel monitoring solutions offered by OMNICOMM for commercial vehicles and other construction equipment?
We have more than 20 years of expertise in fuel management solutions. It includes three key components: fuel sensors with incomparably high-quality and reliability and negligible percentage of warranty claims that decline year to year. They are exceptionally robust, demonstrate 99,5% accuracy in all conditions despite changes in fuel characteristics and does not require servicing for re-calibration, reducing costly vehicle downtime, have highest possible ingress protection rating of IP69k, can work in the hardest conditions.
High-quality terminals able to meet extreme working conditions and maintain uninterrupted data transmission even in areas with incomplete GSM coverage, in conditions of constant shaking and intense vibration, high dust content in the air and extreme weather temperatures (-40o to +85o). The third component - software module provides a comprehensive fuel data analytics that have no analogue on the market. With OMNICOMM online monitoring system, you will have advanced fuel analytics and report: control fuel level on each vehicle online, fuel use on the route, refueling and draining, detailed statistics, deviation from the rated fuel consumption.
The implementation of fuel management system from OMNICOMM makes efficiency comes true: vehicles are operated in optimal mode, without overloads and downtime. The OMNICOMM system records running hours and alerts you when scheduled maintenance is needed, reducing repair costs by up to 15%. The OMNICOMM solution remotely shows the exact amount of fuel left in the tanks. Online monitoring allows you to eliminate equipment downtime caused by a lack of fuel. The work is going according to the schedule, without delays. The OMNICOMM reports contain data on fuel consumption for each piece of construction equipment. Using them, it is easy to calculate the need for fuel resources and timely plan the cost of fuel and lubricants by time/objects.
What are the fleet management solutions introduced by the company?
OMNICOMM's comprehensive IoT solution for monitoring construction equipment allows you to remotely track the movement of special equipment and monitor its operation parameters in real time, including fuel consumption and driving style. Implementation of OMNICOMM gives up to 30% savings in fuels and lubricants, improves safety at construction sites, improves the production of equipment by 30-35%, extends its service life and eliminates misuse. With the OMNICOMM system, construction equipment is distributed to construction sites extremely efficiently, fuel consumption is precisely planned - without surpluses and shortages.
How do you view the trends in adopting various monitoring and control technologies in construction industry?
The construction industry is one of the most actively developing industries and as most of the others is driven by digitalization, IoT and advance analytics. These are key things that can make company to be on top of competitive edge. When you know and can control your fleet including drivers' behaviour, fuel use and leakage, then finally you can save and invest more money to meet your customer's demand.
Companies in this industry are focused on reducing costs through high-quality monitoring of the fleet, performance and control over the actions of drivers.
Telematics solutions that are integrated into business model can ensure advantage of controllable processes in that area. There is a clear demand for the solid integrated solutions, combining hardware and software telematics services, as well as high-quality international support that totally corresponds with OMNICOMM's capabilities and expertise. We provide high-quality reliable integrated telematics solutions for monitoring vehicles and fuels with international support on all continents.
What will drive the demand for monitoring solution in construction industry?
One of the key drivers in the construction industry is the need for comprehensive control over all types of equipment including construction machinery and personnel, which can significantly reduce the cost of maintenance and post-warranty maintenance of equipment, reduce the amount of equipment downtime, solve the problem of the fuel theft and unauthorized flights, optimize the number of vehicles, as well as significantly increase the efficiency of its use.
Rapid growth and development in construction industry as well as high competition requires getting the maximum ROI in the shortest possible time from implementation of telematics solutions. The expertise of the OMNICOMM team and the comprehensive support of wide international partner network allow us to demonstrate an average return on investment in the construction industry of about 3-5 months, depending on the depth of implementation of telematics solutions.
How do you look at the demand for your solutions? What are your expansion plans?
The digitalization drives many industries, and we see very positive market development for the telematics services and especially for fuel management system. Over 20 years, we have been providing this deep expertise and actively developing our business in international markets like India, Africa, Brazil and Mexico. Our newly opened production facility in Ho Chi Minh City (Vietnam) serves with product supply all over the world, ensuring six stages of quality check and certified according to all requirements of the industry. Our strengths are our technology, analytics, quality, and continuous improvement. We have our own development center, and invest 20% of profit yearly to R&D. So, we are very optimistic about future development and committed to serve our customers with the best quality and value solutions in telematics space.
Hits: 1