Customised AAC PLANT SOLUTIONS
As a leading enterprise in the Autoclaved Aerated Concrete (AAC) industry, Keda Suremaker has always been committed to providing customers with holistic AAC plant solutions, which depend entirely on all the relevant factors and prevailing conditions, such as available space, production capacity, climate, packaging, logistics, budget, and much more. Nowadays, increasingly smart AAC plants powered
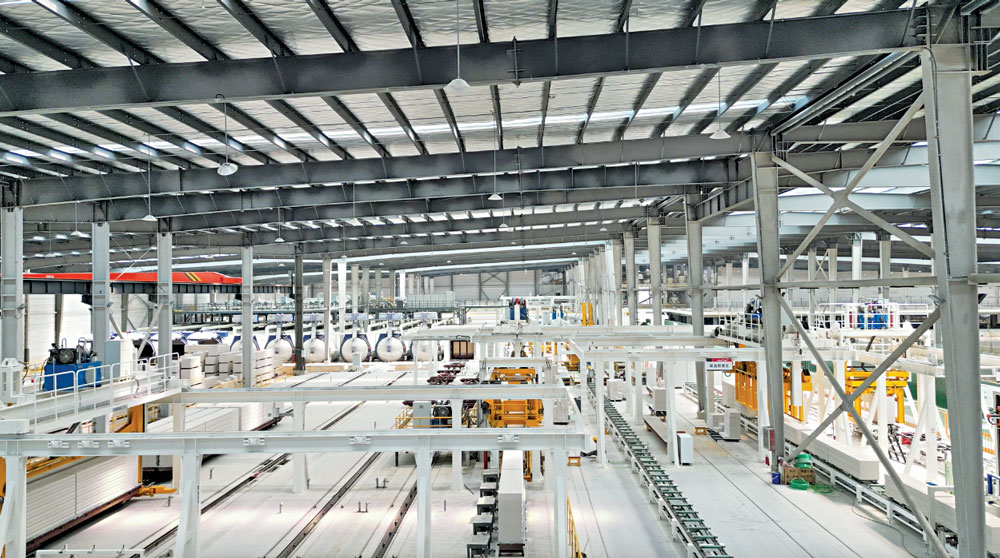
As a leading enterprise in the Autoclaved Aerated Concrete (AAC) industry, Keda Suremaker has always been committed to providing customers with holistic AAC plant solutions, which depend entirely on all the relevant factors and prevailing conditions, such as available space, production capacity, climate, packaging, logistics, budget, and much more. Nowadays, increasingly smart AAC plants powered by Keda Suremaker are commissioned for production. How to improve production efficiency and obtain high-quality products more flexibly has always been an important topic. Keda Suremaker has established excellent long-term relationships with customers in order to jointly confront challenges and constantly optimise technology through practical research.
Keda Suremaker can deeply understand. For the new projects, Keda Suremaker hopes to make innovative adjustments in equipment and design planning to optimise functionality, which is strongly supported by HGA. In March 2022, the two HGA AAC plants based in the Anhui and Guangdong provinces were put into production.
Customised packing in the HGA Anhui AAC plant
HGA Anhui is an important strategic pivot of the HGA Group in East China. The plant is located in the Sanshan Economic Development Zone, Wuhu City, Anhui Province, China. HGA Anhui plans to produce 800,000 cubic meters of AAC panels and blocks annually, as well as provide integrated services and total solutions for green building systems.
The Keda Suremaker technical team and the HGA management team communicated and discussed the specifics around the HGA Anhui project several times before putting forward some customised ideas and design requirements for the packing section of the plant. In particular, the following three aspects needed to be considered:
- The plant is a double-line facility with 20 autoclaves. All the equipment are installed in one large workshop, and the packing section of the two production lines is concentrated in the middle of the workshop, which makes the space for forklift transport more constraint.
- In this plant, HGA hopes to produce varied sizes of panel products. The plant capacity planning is predominantly based on AAC panels, so the packing volume of panel products is larger compared to other facilities.
- In order to improve the quality of AAC panels, the customer needs to inspect and sort the finished panels.
In response to the demands for panel packing, Keda Suremaker provided the technical solutions discussed in the following.
The clamping machine for the white cake can move smoothly and accurately to the specific position. It is equipped with 15 pairs of collectors with independent ball valves, which is convenient for transporting the blocks and panels produced by the same mould to different conveyor belts. When the collectors are released, the products can immediately be transported on the conveyor to the next station, which provides great savings in operation time.
In order to improve the packing efficiency, two independent panel conveyor lines and a combining conveyor line for blocks are positioned in the packing area. Each panel conveyor line is equipped with many rubber-covered supporters, which help transport the panel in a stable manner and without breakage. The two conveyor lines can be operated separately to speed up production, increase efficiency and meet the needs of high-capacity production.
An additional panel sorting crane and two panel sorting rail pulleys are installed behind the clamping machine. The sorting crane straddles the panel conveyor lines and panel sorting rails. The sorting crane clamps the panel on the conveyor in layers for inspection. AAC panels requiring special post-processing are transported to the sorting chute, from where a forklift truck transports the panels to the post-processing area.
A double-layer conveyor was applied in this project. The lower layer was designed for pallet transport and an upper layer for AAC block transport. It is possible to store a certain number of pallets on the conveyor to reduce the frequency of forklift pallet transport, and also to reduce the floor space for the equipment.
The above design solutions have been well received in the actual production and operation.
Flat cake autoclaving technology in the HGA Guangdong AAC plant
More good news coming from the HGA Group relate to their HGA Guangdong plant, which produced more than 40,000 cbm of AAC panels in March this year. HGA Guangdong is the first prefabricated building component enterprise introduced in the Qingyuan Area, Guangdong. In 2022, HGA Guangdong has set an annual target of producing and selling 330,000 cbm of AAC panels and 100,000 cbm of AAC blocks. Therefore, the breakthrough of 40,000 cbm of panel production in March is undoubtedly a strong support for this target. This project has added many new innovative elements, which has given more confidence to the technical teams of both sides to insist on innovation.
At present, most of the Chinese AAC plants adopt the AAC production technology of the vertical cake autoclaving process. Both Keda Suremaker and HGA Group hope to have a project to explore the effect of flat cake autoclaving with Chinese equipment and technology. Keda Suremaker, as the leading supplier for AAC plant solutions in China, is actively exploring different AAC production solutions. The HGA Guangdong project is a successful example of cake cutting in an upright position combined with a flat cake autoclaving process for white cake separation. The flat cake autoclaving process shortens the actual autoclaving time and ensures an efficient production schedule, based on which mass production of AAC panels is achieved.
The AAC industry is now gradually entering the stage of pursuing higher quality and wider application of AAC products. For this reason, after scientific analysis and market research and based on the successful case of the HGA Guangdong Project, Keda Suremaker has officially launched the AAC plant solution of cake cutting in an upright position - green cake separating - flat cake autoclaving.
In this solution, a new green cake separating machine different from the current technology was launched. The green cake separating machine adopts an intelligent electric mode without hydraulics. With the special design of the structure, the machine can separate panels from both sides of the cake synchronously to save time. Flexible and retractable combined separating heads at the top and bottom can protect the concave and convex grooves of panels without damage during separating. Compared to the traditional design of the green cake separator, the design structure of the Keda Suremaker green cake separating machine is more conducive to cleaning and maintenance. The green cake separating facilitates steam circulation between panels, especially for the steam curing of thin panels, to meet the market demand for high-quality panel products.
Keda Suremaker provides customers with systematic whole life cycle services for AAC production plants, including raw material test and formula design, layout planning, equipment manufacturing, guidance for local installation and operation, and personnel training to ensure a successful start-up. Nowadays, Keda Suremaker's AAC plants are in operation all over the world. The technology supplier is devoted to benefiting its customers with the practical know-how of AAC production and provides considerable services to support successful operations.
Hits: 1