Engineered doors: the way forward
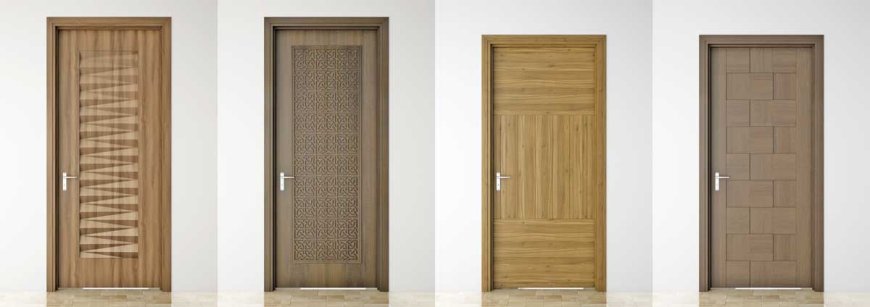
You must be aware that there are four standards for manufacturing Flush doors. These are:
IS 2202 (Part 1): 2023 wooden flush door shutters (solid core type) part 1 plywood face panels
IS 2202 (Part 2): 2022 wooden flush door shutters (solid core type) part 2 particle board, high density fibre board, medium density fibre board and fibre hardboard face panels
IS 2191 (Part 1): 2022 wooden flush door shutters (cellular, hollow and tubular core type) Part 1 plywood face panels
IS 2191 (Part 2): 2022 wooden flush door shutters (cellular, hollow and tubular core type) Part 2 particle board, high density fibre board, medium density fibre board and fibre hardboard face panels.
Performance criteria irrespective of the way the doors are made and irrespective of the external or internal contents of the door remains the same. The myth that solid timber infilled doors are better than other technologies is not a reality.
Flush door shutters can be now classified in two grades as follows:
a) BWP (Boiling Water Proof) Grade — Such flush door shutters recommended for use at humid and dry locations.
b) MR (Moisture Resistance) Grade — Such flush door shutters recommended for use at dry locations only.
All the four types of flush doors are covered under mandatory quality control order which will necessitate door manufacturers to have ISI mark on all the doors manufactured and sold by them with effect from 28.2.2025.
The flush doors have to undergo the following tests
Type Tests — Tests carried out to prove conformity with the specification, which are intended for product/type approval of a given construction or a prototype of door shutters. These comprise: Dimensions and squareness test, General flatness test, Local planeness test, Impact indentation test, Flexure test, Edge loading test, Shock resistance test, buckling resistance test, Slamming test, Misuse test, Varying humidity test, End immersion test, Knife test, Glue adhesion test, and Screw withdrawal resistance test.
Acceptance Tests — Tests carried out on sample taken from a lot passing type tests for the purpose of acceptance of the lot on a batch to batch basis: Dimensions and squareness test, general flatness test, local planeness test, slamming test, end immersion test, knife test, and glue adhesion test.
Considering the simplicity of doors made with engineered material which offer same performance and superior surface finishes the door industry and furniture manufacturers should look forward to making doors the 100% engineered material with IS 2202 Part 2 or with IS 2191 Part 2 marking which allows them to use the popular MDF/HDF skins as well decorative skins with modern matching edge band options.
Engineered doors using engineered material are very easy and simpler to manufacture because manufactures stand below advantages: No search of wood; No need of seasoning of timber; No need for chemical treatment; Minimal heat energy costs; Minimal labour costs; Increased production; Superior finish; and eco-friendly and green product.
These types of flush doors use high content of engineered material which are manufactured from saw mill wastes, shavings, lops and tops etc, converted into the engineered infill as well as the HDF/MDF used as skins.
The door industry is sure to take advantage of getting ISI certifications using engineered modern materials and go for certifications under IS 2202 part-2: 2022 and IS 2191 Part 2: 2022. Increase productivity leads to increased profits and assures customers of minimal benchmark of quality.