INDIA - a new LAND of OPPORTUNITY for AAC INDUSTRY
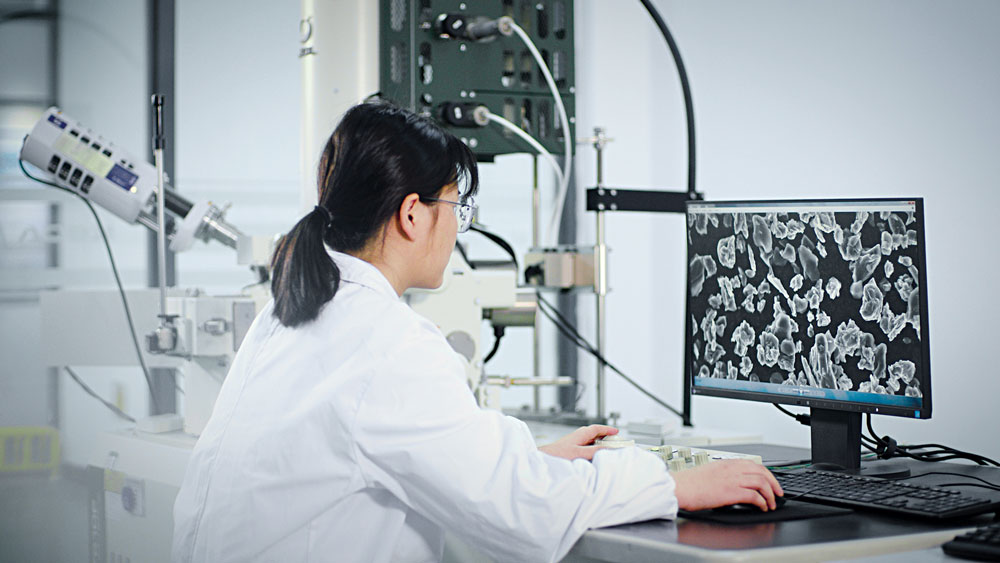
As a leading autoclaved aerated concrete plant solution supplier in China, Keda Suremaker advocates providing holistic autoclaved aerated concrete (AAC) plant solutions with regards to raw material analysis, plant planning, R&D, manufacturing, construction guidance, production management, training and marketing. In addition to high-quality equipment, achieving excellent performance of AAC products requires experience in the production processes and mature quality control procedures.
In recent years, India has become a new land of opportunity, with population and economic growth contributing to the continued rapid development of the country's construction industry. The Indian economy is highly dependent on infrastructure and various government policies. With the national government's continued focus on green building materials, the market for AAC blocks is simultaneously expanding. The quantities of raw materials used in AAC construction are only about one-third of the quantities used for other building materials. In addition, most government departments and construction companies are now moving towards AAC as their preferred building material because it offers many additional advantages, such as resistance against fire, insects and earthquakes, as well as sound insulation, which makes this technology the most convenient and cost-effective solution in the construction process. Since traditional red clay bricks are a major cause of air pollution and soil degradation, the government has continuously been working at reducing their use. All these factors promote the production of AAC blocks in India.
Featherlite Buildcon Private Limited is a prominent company that is involved in manufacturing and retailing a supreme quality range of AAC blocks. “We started our journey in 2015. And looking back, it has been an awesome ride, obtaining worldwide leading technology and importing the right machinery from Keda Suremaker. The major reasons why we decided to open our AAC block plant were the growing government restrictions on the use of red clay bricks and the emphasis on using green, energy-efficient construction materials. The growth in infrastructure projects and construction activities required blocks of high quality and there was no plant nearby as the raw materials required were not available within a radius of 500 km from our site. Establishing a plant for production of earthquake-resistant products in a seismic zone further attracted us towards the idea. We started with intensive research, which included visiting many plants across India and China, performed a market analysis of the availability of raw materials, and took the raw materials to the Keda Suremaker laboratory for evaluation. Finally, after all these measures, we decided to establish an AAC production plant in Kishanganj, Bihar, with the focus on procuring the best machinery available - a machine that manufactures products of the highest quality with negligible waste,” Kuldeep Dhanuka recalls.
Autoclaved aerated concrete is based on the calcium-silica hydration reaction. Apart from traditional sand, there are many types of solid waste that can be used to produce AAC, such as slag, tailings, ceramic tailings, etc. The most common solid waste is fly ash. Large amounts of fly ash are available on the Indian market and the utilization of solid waste is important for environmental protection. When Keda Suremaker approached Featherlite, Keda´s Experiment Center provided its customer with professional raw material analysis and mix formulation testing. The Indian market places a lot of emphasis on the strength of the products, and the market requires varying levels of product quality and product application. In addition to offering experience and guidance on production processes and related technical matters, Keda Suremaker supplies cutting systems that ensure the accurate cutting of products to the required dimensions.
Keda´s intention is to help its customers to produce high-quality precision products, which will lead to a brand that will last a hundred years. Even though the Featherlite Buildcon project has been in operation for many years, Keda has always maintained friendly contacts to share process technology and market information.
The Featherlite Buildcon AAC product is designed with a density of 600-650 kg/cu m and a strength of 4.75+ MPa and is manufactured to precise dimensions. Equipped with the finest laboratory, Featherlite Buildcon ensures that each block leaving the manufacturing facility adheres to global standards of quality and performance, while also ensuring less wastage for smart construction. The blocks have consistent quality, since all the raw materials go through proper testing and because the whole production process is monitored by highly trained staff, which is also a major strength of Featherlite Buildcon. The autoclaving process, which plays a major role in the quality of AAC blocks, is very closely monitored. The plant provides large storage capacity to keep stock of finished products, with a covered area of 5,500 sq m. Consequently, the company can supply blocks throughout the year, irrespective of weather conditions. Prior to dispatch, the quality control department properly checks all batches of finished products. Due to their quality and 'customer first' approach, the company now operates in five states in India, including West Bengal, Bihar, Assam, Sikkim, and Jharkhand, and is also exporting their products to three foreign countries, namely Bhutan, Nepal, and Bangladesh.
Keda Suremaker's AAC plant solution can provide a complete project service roadmap, which is divided into four parts as follows:
Part 1: Raw material and planning
- Organize the expert group to visit the project site and plan the plant layout according to site conditions and raw material resources.
- Configure the appropriate range of equipment and conduct an investment feasibility study according to the expected capacity and automation level.
Part 2: Production and logistics
- Develop a reasonable production plan to ensure delivery schedules.
- Provide various options for packaging and logistical solutions related to the specific requirements of the project.
- All major equipment must be factory-commissioned to ensure reliable quality.
Part 3: On-site installation and commissioning
- Assign an experienced project service team to the local site before the first equipment arrives. Cooperate with the on-site construction team to ensure smooth progress of the project.
- Provide full support for the whole plant planning, equipment installation, electrical commissioning, and process solutions. In addition to the local service team, provide 24-hour online remote service.
Part 4: After-sales service and training
- Provide training and consulting services for customers throughout the project life cycle, including but not limited to equipment operation, safety instructions, equipment maintenance, and process FAQs.
- Keda Suremaker Engineering Service Center is responsible for spare parts and after-sales support to ensure that after-sales needs are always met.
Hits: 3