Why India needs more Offsite Modular Homes?
The country's construction industry has not kept pace with the growing housing needs of India's burgeoning cities.
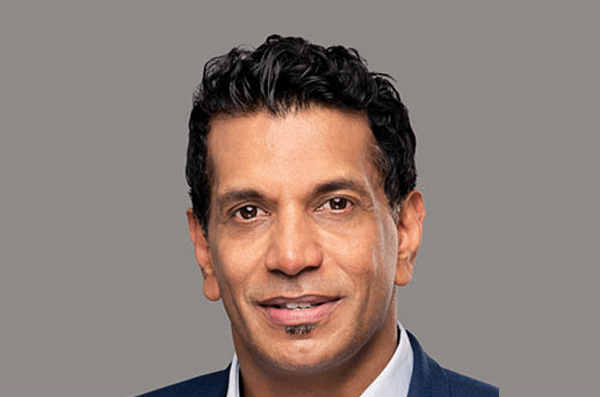
[vc_row][vc_column][vc_column_text]Nejeeb Khan,
Head Design & Business Strategy India,
Katerra.[/vc_column_text][vc_column_text]India has an estimated urban housing shortage of 18.8 million and growing according to recent industry reports. The country's construction industry has not kept pace with the growing housing needs of India's burgeoning cities. A quality, affordable home is still a proverbial and unattainable dream for most of India's population.
To address this, The Indian Urban Ministry has proposed to provide housing to everyone through several initiatives such as 'Housing for All by 2022', 'Affordable Housing' and 'Smart Cities' which would require constructing approximately 30 million houses and building close to 98 smart cities respectively. To achieve this colossal feat within the promised timeline, India would need innovative and technology-driven construction and design methods that can help build houses at least three times faster than the current traditional way. In such a scenario, DfMA and offsite modular construction will be critical technologies to construct homes more quickly and sustainably than conventional construction.[/vc_column_text][vc_column_text]Originating in Europe after World War II, offsite modular construction has now become a common trend across many parts of the world. Testimonies to this are the world-famous structures such as the BurjKhalifa in Dubai and the Sydney Opera House in Australia. Many Indian real estate developers are now embracing the advanced modular technology to build affordable homes. These developers are experimenting with constructing complete home units, an entire kitchen or a bathroom equipped with electrical and other plumbing fittings offsite in a factory environment. These completely ready rooms are transported to site and assembled, saving 50 per cent construction time.
Globally offsite manufactured, modular buildings are gaining prominence, and the market is expected to reach US $135,945.6 million by 2023, according to a recent report by Market Research Future (MRFR).[/vc_column_text][vc_single_image image="33792″ img_size="full"][vc_column_text]Offsite Modular Construction - The concept
Offsite Modular Construction is a combination of beautiful designs with high-quality, controlled manufacturing procedures. The work is carried out in two stages - first, components are manufactured in an automated assembly line production inside factories.
Completed and quality tested components are then transported and installed on the building site. This method has provided a significant shift from the traditional time-consuming and expensive model of construction. Besides, since components are factory manufactured, they are better quality and consistent, unlike manually produced elements. Multi-level buildings can now be built within 90 days, using approximately 20 per cent less material and space. [/vc_column_text][vc_column_text]Advantages of Offsite Modular Construction
- Reduced cost: Offsite construction helps reduce construction, workforce, material, water consumption, and labor cost significantly, thus making it cost-effective.
- Environment-friendly: Waste generated during construction can be managed much more effectively since most of the building gets completed in a controlled environment inside a factory.
- Strong structure: The modules that make up a building are more factory manufactured and more durable than those built traditionally. Offsite manufactured buildings not only need to meet design requirements but also withstand transport loads as the structures are transported to the site where the building will be constructed.
[/vc_column_text][vc_column_text]
- Shorter construction time: Since offsite modular buildings are driven by technology, the construction takes places quicker than traditional construction. Producing high-quality and custom-built buildings and facilities also give the developer a better control over the project timelines and hence, serve his customers better.
- Consistent quality: The sub-assemblies of the structure gets a uniform quality, as manufacturing takes place in a controlled manufacturing environment by following specified standards.
- Audibility: The sound qualityof modular homes is much better than the houses built traditionally. In traditional homes, sound travels through the walls and ceiling, which is why floating floors are often used to suppress noise. In prefabricated houses, each module is a separate construction. The modules connected in the house are protected from transferring sound from one to the other.
- Better labor management : Offsite construction technology is not labor-intensive compared to the traditional method of construction. This helps in addressing the biggest challenge of the construction industry - lack of skilled labours.
While there is a considerable opportunity for offsite modular construction industry in India, the concept is relatively new among Indian developers and home buyers, posing a challenge for the overall growth of the industry, especially in the housing/residential sector. Offsite construction players need to break the misconceptions and create more awareness and education about the effectiveness of this modern technology. Adopting such technology already proven in countries like China, USA, Australia, Middle East, and Singapore will be the only answer to India's growing housing shortage.[/vc_column_text][/vc_column][/vc_row]
Hits: 1929